Broughton's Regulatory Operations Manager, Emily Saunders, explains what cold-pressed CBD products are and why they are currently exempt from the UK and EU Novel Food Regulations.
Sustainable asset use in laboratories
Pharmaceuticals
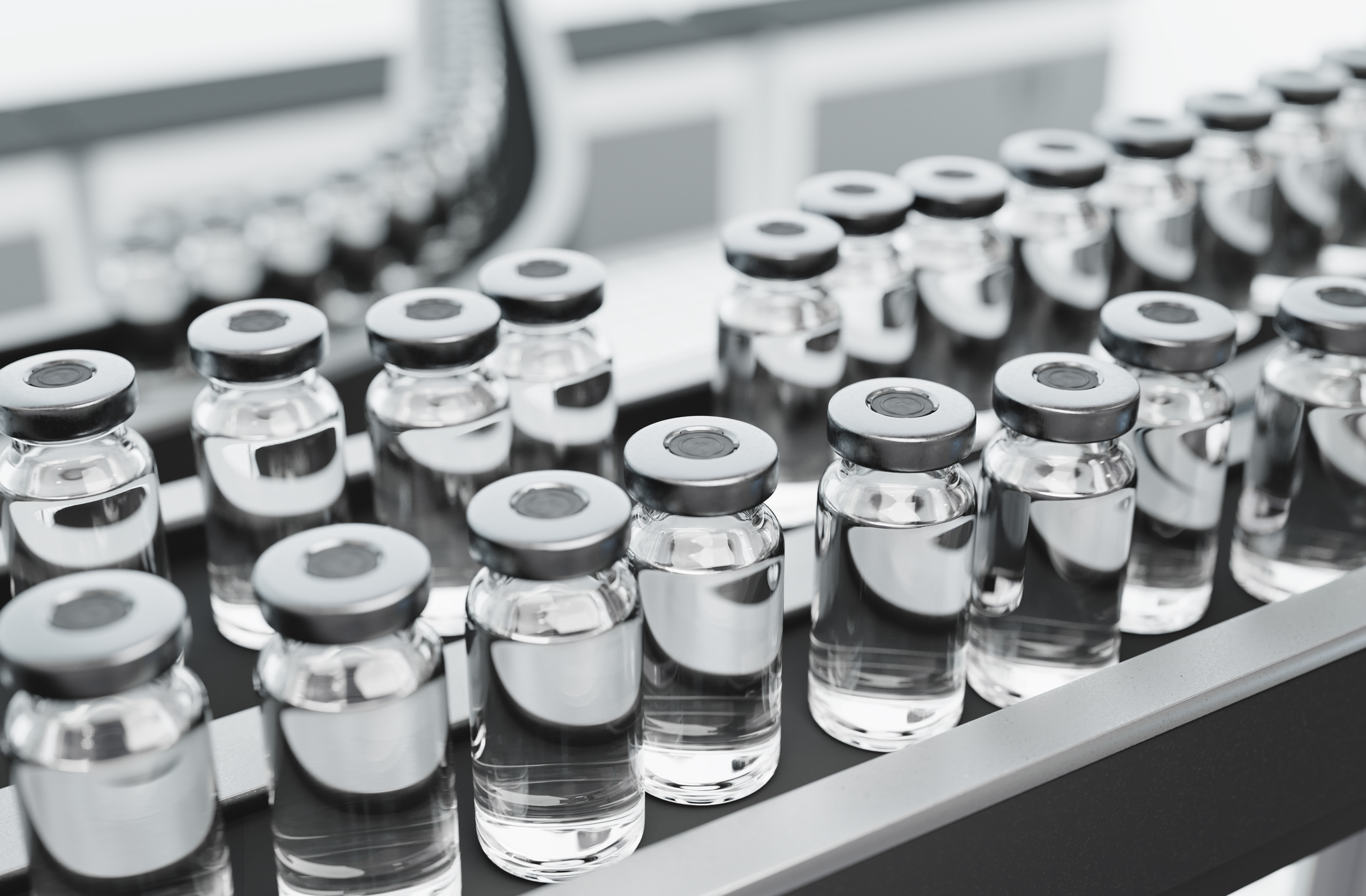
Mar 13, 2024 | Published by Katie Harrison
Pharmaceuticals
When considering sustainability in the laboratory, an obvious starting point is waste reduction or recycling plastics, water, and solvents. Less consideration is typically given to the influence of asset management on sustainability, but a reliable, communicative fleet of instruments has the power to improve efficiency and sustainability simultaneously. Here, Katie Harrison, Operations Services Manager at Broughton, shares some advice on sustainable asset management in the laboratory.
The work that laboratories perform is invaluable, but also resource-intensive. According to University College London, a typical laboratory uses three to ten times more energy per square meter than office spaces.
Manage, monitor and maintain
A simple step to improving sustainability in a lab is to ensure you have a reliable, up to date inventory. This can help reduce the unnecessary purchasing of consumables and parts, some of which have expiry dates that render them unusable if not well-tracked. A 2020 survey conducted by the publication Chemical and Engineering News on behalf of MilliporeSigma of nearly 1,000 researchers found that more than one in five said they lose at least 10 per cent of their monthly inventory due to spoilage and expirations. Making the best use of available consumables can reduce the carbon footprint associated with surplus deliveries and reduce waste.
Equipment maintenance is another way to make the most of what’s already in the building. Maintenance helps keep instruments healthy, extends service lives, and improves energy efficiency. Most instruments give key warning signs ahead of a fault or failure, be it pump pressure profiles of an HPLC or temperature profiles on a cold storage unit. Having automated monitoring and notification of these early warning signs will enable predictive action to be taken.
Equipment that breaks down regularly can have a significant environmental impact through wastage associated with downtime and repeat analysis and repair. Implementing trending and tracking means problematic equipment can be identified and possibly decommissioned, while supporting the concept of reliability-centered maintenance.
Finding the right balance between repairing and replacing equipment can be difficult. While a throwaway culture is wasteful, keeping an older instrument going uses more energy, requires regular repair, and can result in unique servicing/maintenance requirements that can be damaging too. For example, data from Shimadzu shows that the new Nexera ultra HPLC enables a 68 per cent reduction in power consumption on standby compared with a previous model.
Succession planning is therefore important to regularly take stock and plan for the future. If you own ten balances and more than half are over 15 years old, it's probably time to start planning for the retirement and replacement of this instrumentation. When doing so, take the opportunity to make changes that support your sustainability goals rather than just replacing like for like.
Digitalise
Connecting multiple systems in a workflow can help speed up processes to reduce energy use, improve throughput, and provide data intelligence that improves laboratory operations. According to the Agilent Lab Manager survey, in 2020, laboratory instruments were only running 35 per cent of the time — quantifying the downtime of your instrumentation can enable better scheduling, so laboratory managers can optimize usage and reduce the number of instruments required.
While going paperless can be difficult in a 21CFR compliant industry, it is possible. Most modern equipment is supported with software packages that enable users to store data electronically in a compliant way, reducing paper use. For example, Chromeleon, OpenLab, and Empower are software packages that can help digitalize data management.
Build a sustainable supply chain
When selecting partners, talk openly about sustainability initiatives and goals. Building a sustainable supply chain can have a cumulative impact on your sustainability goals. Some suppliers will have sustainability fact sheets available on their website specific to equipment types, which can help in the decision-making process. These fact sheets share information on the use of recycled materials, whether the facility the instrument is made in relies on power from fossil fuels, and equipment features that reduce energy consumption, such as reduced energy standby modes.
Simplifying your supply chain so that you are working with a single manufacturer for each instrument makes it easier to train analysts and simplifies analytical method transfer. This approach makes developing experts in one system much easier than multiple platforms, reduces the need for different consumables and parts, and makes servicing more efficient and sustainable.
While laboratories are up to ten times more energy intensive per square meter than offices, numerous steps can reduce this. Asset management, waste management, and your supply chain can result in an efficient laboratory with a reduced carbon footprint.
Are you looking to work with an experienced analytical testing team that cares about sustainability? Visit our website.
*Article originally published in Laboratory News