Heated tobacco products (HTPs) are continuing to grow in popularity globally. The market’s worldwide value grew by $3.7 billion from 2022 to 2023, with Euromonitor International expecting it to hit...
What is the Tobacco Product Manufacturing Practice (TPMP)?
Nicotine
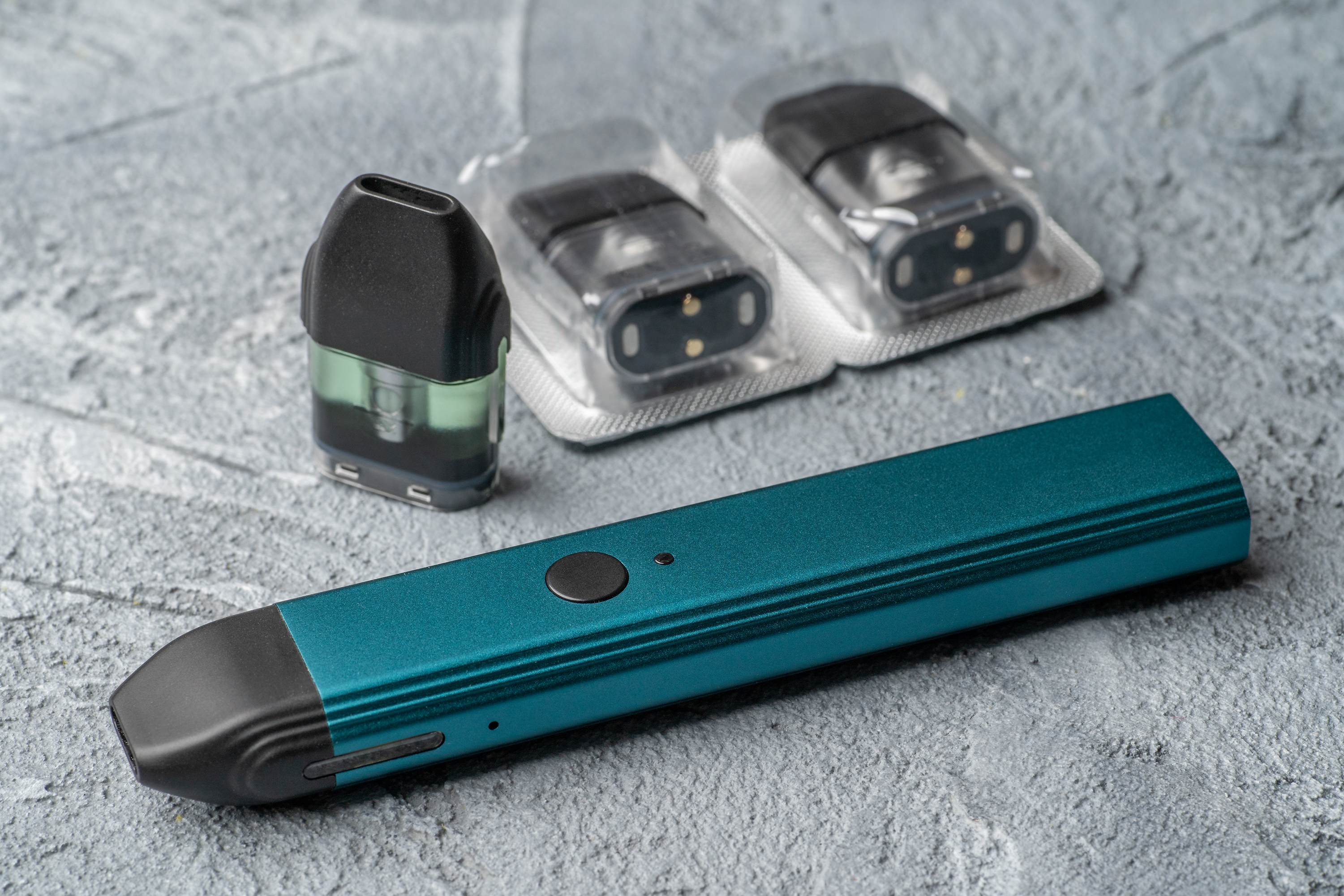
Mar 30, 2023 | Published by Paul Barr
Nicotine
The U.S. Federal Drug Administration (USFDA) announced its long-awaited proposal to raise the standards for tobacco product design, development, and manufacturing to strengthen the protection of public health. This regulation will apply to next-generation nicotine delivery products such as ENDS, e-cigarettes, heated tobacco, and modern oral pouches, as these are classed as tobacco products under U.S. regulations.
The 21 CFR Parts 1100, 1107, and 1114 ruling of May 2021 provided a broad outline of the requirement for the information to be provided by tobacco product manufacturers. Those requirements were flexible and general in their nature. The proposed Tobacco Product Manufacturing Practices (TPMPs) for finished and bulk tobacco products bring much-needed clarity and rigor to the process of bringing a tobacco product to market in the U.S.
The TMPS breaks down into five different areas, and our Consultant, Paul Barr has created a summary of each section based on the 90-page proposal.
Quality Processes and Systems
In a move that will bring tobacco product regulation closer to that of medicinal products and medical devices, the USFDA has brought industry standard practices into a unified standard. Whilst maintaining some degree of flexibility, the standards set out in the proposed TPMP are akin to GMP standards that are well established in other regulated arenas. There is also a greater emphasis on ensuring the manufacturer’s business systems and infrastructure are suitable for the production and mass market supply of safe products. The requirement for documented organizational and personnel competence directs the manufacturer to provide evidence of the professional qualifications, training, and experience needed to carry out their designated function(s).
Infrastructure
The proposed rule emphasizes the need for buildings, facilities, and equipment to be suitable for the production of the tobacco product in question. Buildings must be designed, constructed, and located appropriately to facilitate a safe environment for the personnel and the tobacco product being manufactured, packed, or stored. The proposed rule mandates keeping records to evidence the management of cleaning, sanitation, and animal/pest control activities under approved protocols and reports. The proposed rule requires the manufacturer to maintain and monitor environmental controls appropriate for the tobacco product being produced, packed, or stored. These include lighting, heating, ventilation, and cooling (HVAC), waste management, plumbing and water management, cleaning, sanitation, and pest control.
The equipment being used to produce the tobacco product must have documented evidence of a design specification and that the construction is suitable for the intended use. Maintenance and calibration must be evidenced to ensure equipment is working in accordance with its specification at the time of any tobacco product production activity. The proposed rule also mandates that the manufacturer identify production lines and equipment to prevent mix-ups and contamination.
Design and Development Control
The proposed TPMP rule requires that each finished and bulk tobacco product manufacturer must establish and maintain procedures to control the design and development of each finished and bulk tobacco product. These procedures include the need for risk management through every aspect of the design and development process, requiring detailed verification and validation of specification and implementation. There is also a need to document and record design changes to identify why changes have been made in support of protecting public health.
Master Manufacturing Record (MMR)
The proposed rule brings a requirement for MMR. This is a document or designated compilation of documents containing the established specifications for a tobacco product, including acceptance criteria for those specifications, all relevant manufacturing methods and production process procedures for the tobacco product, and all approved packaging, labelling, and labels for the tobacco product; this is similar to the Batch Production Record (BPR) for medicinal products in the USA Every tobacco product manufacturer must establish and maintain a master manufacturing record (MMR) for each finished and bulk tobacco product they manufacture for distribution.
The MMR must include the specifications (including any physical, chemical, and biological specifications) and acceptance criteria for those specifications. It must identify all packaging, labelling, and labels for the tobacco product’s sale and distribution. The manufacturing methods and production process procedures and controls must be documented in the MMR so that the manufacturer can establish and maintain procedures for the review and approval of the MMR documents by a designated, qualified individual; this is a move towards creating a role similar to the Quality Control Unit (QCU) in USFDA regulations under CFR Part 211.192.
Customer Complaints and Returns
Whilst the management of customer complaints and returns was included in the May 2021 ruling, the TPMP provides more detailed requirements for the manufacturer to manage complaints, returned products, non-conforming products, and any associated reprocessing or rework activities. The manufacturer must establish and maintain procedures for receiving, evaluating, investigating, and documenting all complaints. The procedure must ensure that all complaints are handled promptly and uniformly, evaluate the root cause (design, process, or misuse), and the appropriate investigations to determine corrective action(s) are conducted. All aspects of this process require documented evidence by competent personnel.
Summary
At Broughton, we understand first-hand how challenging it can be to take a product through the PMTA process. We have assembled a team of industry and regulatory experts to help guide you through your entire submission journey, ensuring compliance with the rules and guidance offered by the US FDA. Our knowledge of the PMTA pathway, our vast GMP experience in Pharmaceuticals, and our dealings with international regulatory inspections (including USFDA) demonstrates that Broughton is ideally positioned to support companies in implementing this new regulation.
Visit our website to find out how Broughton's testing services can support your business in this area.